The motion is controlled by the rolling elements along the linear guide. Linear motion guides are essential components in many applications across a wide range of industries. CNC machining, 3D printing, packaging, assembly lines, positioning devices, conveyor systems, automated systems, robotics, medical equipment, aviation equipment, automotive components, and more all use linear guides to facilitate smooth and precise motion. Linear guides play a pivotal role in facilitating precise linear motion, and selecting the right linear guide can significantly impact the performance and longevity of your equipment. Before selecting a linear guide, it is important to understand exactly what your needs are.
Types of Linear Guides
There are several types of linear guides, all of which can be used in various configurations. Some linear guides use ball bearings, some use rollers, and some use sliding elements. There are advantages to each type of linear guide, and when making the selection, it is important to consider the needs of your application.

Linear guides that use linear ball bearings have low friction, a long lifespan, and high accuracy. Linear ball bearings are the most popular type of rolling linear bearings. The ball bearings move with a carriage along a linear rail, and the recirculation of the balls provides many advantages in precision and reduced friction in linear motion. For applications that require precision in linear motion, linear guides that incorporate ball bearings are the standard.

Roller bearings are similar to ball bearings in linear guides, but instead of recirculating balls, the roller enclosed within the carriage is cylindrically shaped. These rolling elements have a higher load capacity, better rigidity, and greater impact resistance compared to ball bearings, but they also have a higher degree of friction and lower precision than ball bearings.

Plain bearings are not rolling elements at all, but rather rely on slides for their linear motion. The simple design provides a cost-effective way to incorporate linear motion into an application. Plain bearing linear guides do have lower lubrication requirements than rolling elements and are often available in self-lubricating options.
Components of a Linear Guide
A linear guide consists of three main components: the linear rail, the rolling or sliding element that bears the force of the load, and the carriage in which the rolling or sliding element is contained. There are various options for each component.
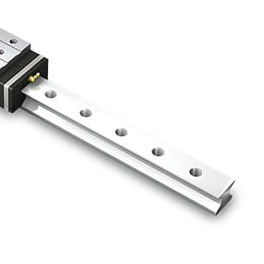
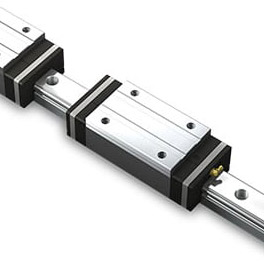
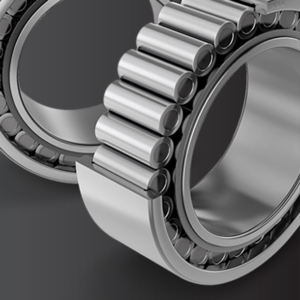
Selection Criteria for Linear Guides
When selecting a linear guide, it is important to look at the needs of the application with regard to load capacity, speed and acceleration requirements, precision and accuracy needs, and environmental factors. Every linear guide can be customized for the specific needs of the application, but careful consideration must be given during the selection process.
Load Capacity: For any engineering design, determining load capacity is important. Linear guides are able to handle high load capacity. The dynamic load calculations are crucial to avoiding failure once the linear guide system is integrated. Load capacity is calculated for both dynamic and static loads. Static loads are the load on the system in a fixed, unmoving position, while dynamic load refers to how the load can be moved through the system. If the load is calculated incorrectly, the system can see increased friction, low precision, and even the failure of the rail. As linear bearing rails are available in a variety of load capacities, it is important to understand the needs of your application before settling on your selection. The load capacity of a linear guide will depend on the size range as well as a number of environmental considerations. It is important that the load is distributed evenly across the rail and rolling elements. Ensuring the load is evenly distributed will help reduce stress on the linear guide system that can lead to premature failure.
Speed and Acceleration: High speed motion is a requirement for applications where throughput is a critical factor, such as packaging or assembly. These systems are typically designed for stiffness and high load capacity, as well as speed and acceleration capabilities. While speed and acceleration are related, focusing solely on one or the other when implementing a linear motion system can be limiting. Speed will have a role in defining the lifespan of a linear motion system incorporating linear rails. Going over the maximum or recommended speed can lead to wear and tear on the linear guide. In addition, if excessive speed continues, it is even possible to break components of the system. When the speed of a linear motion system is needed for a specific application, there are ways systems can be designed for higher speeds. However, maximum speed alone without understanding the relation to acceleration will often not solve the issue. Reducing the mass of the linear guide can reduce the force, and therefore allow for increased acceleration capabilities. Using different materials can help to reduce the mass of the system, which can help optimal performance.
Precision and Accuracy: A high degree of precision is one of the primary benefits of using a linear guide system, but different applications have different requirements. Understanding the precision and accuracy needs of the application is important when selecting a linear guide. Different applications have different tolerances for precision. Accuracy, and more specifically, the need to maintain high degrees of accuracy over time, are also important when selecting a linear guide. Applications that require high accuracy, such as CNC, robotics, and material handling, will need a linear bearing rail based on the precision standards required.To maintain accuracy over time, the guidance system will need to be installed correctly initially and maintained throughout the lifespan. Applications that do require a higher degree of precision will need to have more care during the installation and mounting process to ensure optimal precision during operation of the linear guide system. Having the system mounted with precision will ensure that the linear guide will continue to operate with a high degree of accuracy over time.
Environmental Factors: The environment in which the linear guide is installed can have an impact on the effectiveness and efficiency of the linear guide. In certain environments, different choices need to be made during the selection process.
- Temperature and Humidity Considerations: Temperature and humidity concerns are a factor when selecting a linear guide. Sealing methods are nearly always used for environments that face a high degree of humidity. Most linear guides are only rated for continuous operation at certain temperatures. However, customized linear guides can be implemented for environments where high temperatures and humidity will be a factor. Different materials can be used that have higher temperature tolerances.
- Corrosion Resistance: Most linear guide components are designed to resist corrosion. For operating environments where corrosion is more of a concern, additional steps can be taken to resist the impact of corrosion. The first step to corrosion resistance is to address the parts of the system that are directly exposed to the environment. These components can be made with corrosion resistant materials or have a corrosion resistant coating applied. Plating the surfaces of the linear guide that will be susceptible to corrosion can often be enough to resist it.
- Cleanroom Applications: While in most applications the concern is with keeping contaminants out of a linear guide system, in a cleanroom application, it is more important to keep the linear guide system itself from introducing contaminants. Many industries have some applications that will need to be carried out in a cleanroom, such as aerospace, pharmaceutical, food and beverage, semiconductor, and electronic assembly. In a cleanroom, friction can introduce contaminants, so it is important that any linear guide device has minimal friction during use. Lubrication can help in reducing friction, but care must be taken not to introduce the lubrication particles into the cleanroom atmosphere. Seals are effective in reducing contamination.
Installation and Maintenance
When using linear guides, proper installation and maintenance are crucial for both safety of the user and effectiveness and efficiency of the guide itself.
Installation Best Practices
Linear guide systems are relatively straightforward to install, but this does not mean that installation can be done carelessly. Without proper installation, a linear guide system is far more likely to fail, which can cause issues in the application itself. When implementing a linear guide system, it is important to follow installation best practices. Proper alignment and careful mounting are critical. In addition, safety precautions should always be taken when installing a linear guide.
Alignment Procedures
It is important to align your linear guides properly for optimal performance and efficiency, as improper alignment can cause uneven load distribution. While some linear guide systems can tolerate imprecise mounting, all linear guides will be more efficient when correctly aligned, and proper alignment is necessary for applications that require tight tolerances. Finding the right guide and offset between the rails is the best way to ensure proper alignment.
Mounting Considerations
Linear guides can be mounted in a variety of different ways for different applications. Improper mounting can lead to uneven load distribution, a shorter lifespan, and reduced accuracy. Applications that require greater precision will require a machine referenced edge for each rail to be mounted, while other applications require only one rail to be mounted using a reference, and using a connecting plate to align additional rails. The offset between the rails and carriages will also need to be considered.
Safety Precautions
For maximum safety, linear rails should always be installed and mounted to the specifications indicated. Linear guides should always be installed on a stable and balanced surface for maximum safety.
Lubrication and Maintenance
Although linear guides have relatively low maintenance needs, that does not mean that they can be ignored completely after installation. To keep linear guides working as expected, there is a degree of maintenance, inspection, and lubrication that will need to be implemented.
Proper lubrication techniques will be communicated from the NSK engineers when the system components are purchased and installed. NSK has a uniquely designed lubrication system that will minimize contamination while meeting the lubrication needs of the components. Different linear guides will have different lubrication needs, and the lubrication system can be customized for the specific needs of your application.
Following a regular inspection and cleaning schedule is another element of linear guide maintenance that cannot be overlooked. Preventive maintenance can help determine any potential issues or failures so you can develop a plan to address those issues before a system failure. Different environmental factors will impact how often a linear guide system will need to be cleaned. In harsh environments or environments where contamination can be an issue, sealing the linear guide system can help minimize downtime for cleaning.
When there are issues with a linear guide, several common issues may be to blame, and the engineers can help troubleshoot the problem. Often, any issue with a linear guide will be due to mounting or installation issues and can be remedied by addressing the installation guidelines.
Applications of Linear Guides
Linear guides have applications in nearly every industry, as they are highly customizable and able to be implemented into any system that relies on linear motion.
Manufacturing Industry
From conveyor systems to packaging processes, automated systems to machining, the manufacturing industry relies on linear motion. Linear guide systems are incorporated into a variety of applications within the manufacturing industry. Due to the high load capacity, linear guide systems can be relied upon for robust use, but the high precision and accuracy offered makes them suitable for automated and robotics systems.
CNC Machines
CNC machines play an important role in the manufacturing industry. They are able to provide a level of efficiency, accuracy, and consistency in machining that would be difficult or even impossible to achieve otherwise. There are many different options for CNC machines, and they rely on smooth linear motion to operate. Linear guide systems are critical to keeping CNC machines running smoothly.
Robotics
As more of the manufacturing industry begins to rely on automation and robotics, linear guides can provide the precision of linear motion needed for various systems, such as collaborative robots and automated tasks. Smooth and consistent linear motion will keep these systems running smoothly and consistently with low maintenance needs.
Assembly Lines
Assembly lines rely on smooth, continuous linear motion with low friction and vibration. Linear guides can support smooth motion and have the load capacity for the needs of an assembly line. The low maintenance and durability of linear guides will help minimize downtime and increase assembly line efficiency.
Aerospace and Defense
Precise, lightweight, and low noise and vibration are necessary for any equipment or device used in the aerospace and defense industries. These industries are highly regulated and all equipment must meet exact specifications for compliance and safety. Linear guides can satisfy the demanding requirements of this industry.
Positioning Systems
Linear guides are able to provide the smooth motion and precision needed for positioning systems that are essential to many different applications in the aerospace and defense industries. With customization options, these linear guides can operate in a variety of different environments.
Guided Missiles
Guided missiles require a high degree of precision and accuracy and have little to no tolerance for vibration and noise, making a linear guide system the right solution for their needs. A customized linear guide system will be able to meet all the needs for guided missiles operating in a wide variety of environments.
Aircraft Components
There are many different components in aircraft that rely on linear motion. From the highly technical engine and wheel systems to the motion of the passenger seats, linear guide systems are prevalent in airplanes and other aircraft equipment. Linear guides are durable and dependable enough to be relied on for any aircraft needs.
Medical Equipment
Smooth and precise linear motion is necessary for the medical field. Medical devices and equipment are highly regulated and have very specific standards for vibration, noise, precision, and accuracy. Linear guide systems can provide the low vibration and noise, exceptional precision, smooth motion, and high degree of accuracy necessary for the medical industry.
Imaging Devices
Imaging devices, such as MRIs, CT scanners, and x-ray equipment all rely on smooth linear motion, both for accuracy and precision in imaging as well as for patient comfort and experience. Linear guide systems have the smooth motion, low vibration and noise, and accuracy necessary for successful use in medical imaging devices.
Surgical Robots
Surgical robots are revolutionizing the surgical field, helping medical professionals perform procedures that were once highly invasive or even inoperable. Doctors and technicians who utilize surgical robots rely on the smooth, precise motion and absolute control that a linear guide system can provide.
Rehabilitation Equipment
During rehabilitation, patients rely on a variety of devices and equipment to assist with recovery. Linear motion is used in much of the equipment they rely on for physical therapy and assistive devices. As this equipment needs to be reliable, accurate, and provide smooth operation, linear guides are the right choice for patient use.
Linear guides have a place in numerous applications across multiple industries, including medical equipment, aerospace and defense, manufacturing, and robotics. The benefits of using a linear guide are extensive. Linear guides can provide smooth and low-friction linear motion with a robust load capacity, a high degree of accuracy, the ability to function in a variety of environments, and exceptional precision.
Future Outlook and Industry Innovations
The future outlook for linear bearings and rails is promising, which is driven at least in part by the increasing demand for automation and precision in a wide variety of industries. There have been developments in materials, coatings, and designs that allow linear bearings and rails to be used in an increased number of applications.
There is a growing need for high-performance machinery and equipment, which is developing in tandem with advancements in technology that rely on linear bearings and rails. The ongoing advancements in robotics and industrial automation are driving the demand. Linear rails are crucial in robotic arm movements, 3D printing, and other automated systems that require accurate and repeatable linear motion.
The linear rails market is projected to see substantial growth in the coming years, fueled by this increased demand for automation and precision. With linear bearings and rails providing a precise, quiet, and cost-effective solution, many industries have shifted to linear motion systems relying on linear bearings and rails.
In addition to the increase in demand in general, there is projected to be an increased demand for system solutions, with less design and specification required by the user. Actuators are projected to increase value in linear guide systems by combining multiple linear components, such as linear rails, bearings, and screw drives. As industries continue to innovate, the need for linear bearings and rails will continue to grow, and technological advances will keep the market for these solutions strong. As design and installation time decreases with the advancements in technology, the market growth will increase.
Choosing the ideal linear guide for your project is crucial when you are in the process of designing and implementing a linear motion system. Before choosing the components, it is important to know the exact needs of your application, including the load capacity, precision needs, friction sensitivity, and the environment in which the linear motion system will be implemented. Linear guides can be customized to the exact needs of your application, so before finalizing your plans, consult with the engineering team about the ideal linear motion system. NSK can help you find the right components to build the right system that is able to meet all your requirements. When you are ready to explore a linear guide for your industry, reach out to learn more about how we can help.