In linear motion, an object can only move forward or backward in two possible directions along a linear guide.
Linear motion is a vital aspect of modern motion control in many different industries.
- Robotics
- Manufacturing
- Engineering
- Medical Devices
- Laboratories
- Semiconductors
- Packaging
- Oil and Gas
- Automotive
- Aerospace
For best results in using a linear motion system, the system must be optimized with linear technology that is properly installed, operated, and maintained. By using best practices, smooth and precise linear motion can be achieved, offering increased efficiency and effective processes.
Basics of Linear Motion
Linear motion is one-dimensional motion along a straight line. In linear motion, an object will move in one direction.
According to Newton’s First Law of Motion, an object not affected by any force will continue indefinitely in a straight line.
- Speed is defined as the rate of change of distance, or, more simply put, how much distance is covered in a particular time.
- Velocity is the rate of change of displacement.
- Acceleration is the rate of change of velocity.
In practical applications, linear motion products typically support and guide a mass, allowing it to travel smoothly in one direction.
Principles of Linear Motion
To understand linear motion, one must have a basic understanding of Newton’s First, Second and Third Laws of Motion.
- Newton’s First Law: This law, most important in linear guide systems, is known as the law of inertia. It states that if a body is at rest or moving at a constant speed in a straight line, it will remain at rest or keep moving at a constant speed in a straight line unless acted upon by force.
- Newton’s Second Law: This law states the time rate of change of the momentum of a body is equal in both magnitude and direction to the force imposed on it. The momentum is equal to the product of mass and its velocity. (F = ma)
- Newton’s Third Law: This law of often known as the law of action and reaction. It states that when two bodies interact, they apply forces to one another that are equal in magnitude and opposite in direction.
Understanding and applying the principles of motion and energy have allowed for advances in nearly every field.
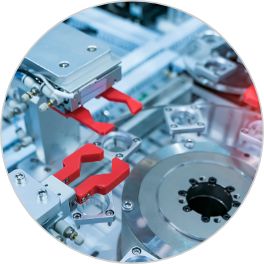
Precision and Accuracy
The ability to reach the goal position as close as possible is considered accuracy, while precision is the ability to replicate the same results relative to each other every time. Accuracy is used to measure the error between the goal position and actual position, and precision is measured by the error range between how far off the positions are from each other when repeated. Linear motion mechanisms provide high precision and accuracy, which is essential for robotics, manufacturing, and medical device applications. Precision linear actuators are utilized in tasks requiring minute adjustments, ensuring meticulous operation control and reliability.
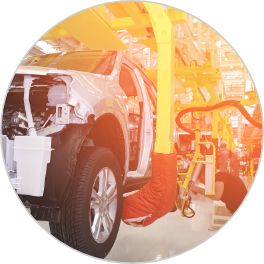
Linear motion systems vary widely in size between varied industries and applications within those industries. Some linear motion systems are highly space-efficient, making them ideal for compact devices like smartphones, cameras, and printers. Miniaturized linear modules are widely used in portable gadgets, optimizing space while maintaining optimal functionality. Miniatured linear motion components can help designers meet even the most stringent space requirements for consumer electronics and medical devices.
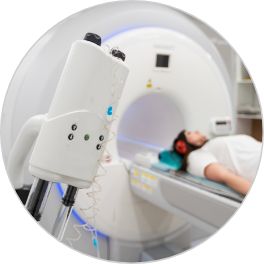
Linear motion systems often consume less energy than rotational systems, making them the sought after choice when various applications require the system to be energy efficient. These energy efficient linear motors and actuators contribute to sustainable technologies, reducing power consumption and environmental impact. When measured, linear motion products can be over 95% efficient.
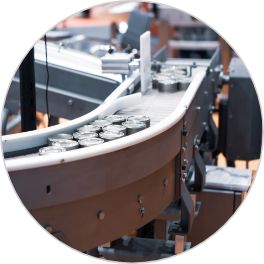
Smooth and Controlled Movement:
Linear motion ensures smooth and controlled movement, enhancing user experience in consumer electronics and automation systems. The smoother the motion, the quieter the system can be during operation, which is ideal for many systems requiring low noise. Devices such as 3D printers, CNC machines, and automated packaging systems rely on linear motion for consistent and seamless operations, resulting in high-quality outputs.
Customization and Adaptability
There are ready-made linear guide systems available for nearly every industry. However, to get the best result for each precise application, customization is available. A custom linear motion system solution can fine-tune your application. Linear motion components can be customized to specific requirements, allowing engineers to design tailor-made solutions for unique applications. Some of the components that can be customized are the materials, contamination protection, coatings, and lubrication. Many linear motion systems are at least partially customized for the exact specifications needed for each application. By working with engineers and designers, a custom solution can be designed to fit the exact specifications and needs for every project.
Applications of Linear Motion
Linear motion guides are everywhere! The applications of linear motion are extensive and reach into many different industries, from relatively simple to intricate and complex systems.
Linear Motion in Robotics and Automation
In robotics, a linear robot is a robot who uses primarily linear motion to provide smooth operating and precision. In automated systems, precision is crucial, and robots using linear motion technology have the ability to provide that level of precision.
- Precision movements: Linear motion is crucial for precise movements in robotic arms and automated systems.
- Pick-and-Place Operations: Linear motion guides the pick-and-place operations in manufacturing and assembly lines.
- Collaborative Robots: Collaborative robots, known as cobots, work alongside humans in manufacturing. The linear motion systems they use enables safe and efficient collaboration between robots and human workers in many different industries.
Linear Motion in Manufacturing Processes
Linear motion and linear rail systems are used throughout the manufacturing process. The smooth and precise motion allows for seamless movement through different stages of manufacturing. Actuators, linear bearings, linear motors, and linear control systems work together in the manufacturing process.
- Conveyor systems: Linear motion plays the primary role in conveyor belts for transporting goods during manufacturing.
- Injection Molding: Linear actuators facilitate precise movements in injection molding machines, ensuring accurate product shapes and sizes.
- Quality Control: Linear motion systems are used in quality control processes, such as automated measurement and inspection systems.
- Machine tooling centers: Linear systems are used in metal cutting, milling, grinding, and other tooling centers during manufacturing.
Linear Motion in Automotive Engineering
Linear motion technology is used throughout the automotive industry. The linear guide systems used in automotive engineering and manufacturing have been designed for dynamic use in tough environments, while the systems used in the vehicles themselves are designed for minimal friction to reduce operating noise. Linear motion systems are used in many different aspects of automotive engineering, including:
- Vehicle assembly: Linear motion technology is used in automotive assembly lines to install components and welding.
- Suspension Systems: Linear motion plays a crucial role in vehicle suspension systems, ensuring smooth rides and stability.
- Steering mechanisms: Linear motion components contribute to the precision and responsiveness of steering systems in vehicles.
Linear Motion in Medical Devices and Healthcare
Linear actuators allow for precise movement and adjustment of medical devices, such as imaging and surgical technology, but also are used in patient care for smooth movement of lifts, hospital beds, and mobility aids. Medical devices are highly regulated and require absolute precision, making linear guide systems a critical piece of the technology.
- Medical Imaging Devices: Linear motion components are used to precisely move parts in medical imaging devices like MRI and CT scanners.
- Robotic surgery systems: Linear motion plays a big role in robotic surgery systems, enabling surgeons to perform delicate and complex procedures with precision.
- Patient care: Linear rail systems are used for applications in hospital beds, patient lifts, and mobility aids, where linear motion ensures ergonomic and safe patient care experiences.
Linear Motion in Laboratory Automation
Precision is crucial for accurate results in laboratory tasks. In today’s laboratories, the use of automation can offer both efficiency and precision in complex tasks. The smallest deviations in control can have a major impact on test results. Fully automated analyzers can provide more accurate results. Linear rail systems are used in these automated technologies.
- Robotic arms: Linear motion components are employed in laboratory robotic arms for precise sample handling and processing.
- Liquid Handling Systems: Linear motion components are used in liquid handling systems, ensuring accurate dispensing and mixing of reagents.
- Analytical Instruments: In analytical instruments, linear motion enables precise, smooth, and repeatable movements for measurement and analyses.
Linear Motion in Semiconductor Manufacturing Equipment
Semiconductor manufacturing equipment is among the most complex and advanced manufacturing equipment across all industries. High precision and exact motion control is paramount in this industry, and linear systems are key to optimal performance.
- Wafer Handling Systems: These robotic systems are designed to automate and facilitate the handling of silicon wafers during semiconductor manufacturing. Linear motion components are integrated into wafer handling systems, ensuring the delicate and accurate positioning of wafers during semiconductor manufacturing processes.
- Metrology Tools: Metrology tools are used for inspecting and measuring semiconductor components with high precision, and linear motion systems are crucial in obtaining the level of precision necessary.
- Cleanroom Automation: In the semiconductor industry, maintaining an ultra-clean environment is essential to prevent contamination of sensitive components. Cleanroom automation systems, equipped with specialized linear motion technology, enable precise movement and handling of equipment within the cleanroom environment. These systems ensure the strict adherence to cleanliness standards, safeguarding the integrity of semiconductor manufacturing processes and the quality of the final products.
Linear Motion in Packaging Industry
Optimal performance is crucial in the packaging industry. Linear guide systems are used throughout the packaging industry, relying on the smooth operation of a well aligned linear rail.
- Conveyor systems: Linear motion is a main component in conveyor systems, with linear guide systems facilitating the smooth and efficient movement of items during the packaging processes.
- Pick-and-place robots: A pick-and-place robot is an industrial robot used for handling and placing products on a production line, usually in high-volume settings. Linear motion components are utilized for these robots, ensuring accurate picking and placing of items in packaging operations.
- Filling and Sealing Machines: Linear filling machines have been a consistent component of production lines, filling containers with accuracy and precision as they pass down a conveyor system. Linear motion components enable precise filling and sealing of products in containers.
Linear Motion in Oil and Gas Sector
The oil and gas sector makes use of linear guides and linear actuators in many different applications.
- Drilling Equipment: Linear motion components are used in drilling equipment for precise movements and positioning during oil and gas exploration. Linear motion shakers can separate out powder and granules in oil drilling. High performance from linear systems is always required in this industry.
- Valve Actuators: The valve actuator is the mechanism for opening and closing a valve. Linear motion is created in valve actuators, ensuring precise control of valves in oil and gas processing plants. For oil and gas well heads, valve actuators can be used to support other major equipment necessary for processing.
- Subsea Systems: Operating underwater, particularly in saltwater, is a challenge for any industry. Linear motion components enable precise movements for remotely operated vehicles (ROVs) and other equipment used in underwater operations. Precision can be achieved without the challenge of liquid immersion.
Linear Motion in Aerospace Manufacturing and Tooling
Linear guide systems have an important role in the aerospace manufacturing and tooling industry, as they are able to provide the reliability and precision demanded by this highly regulated industry.
- Aircraft Assembly: To facilitate smooth and quiet operation, engineers incorporate linear motion components in aircraft assembly lines, ensuring precise alignment and fitting of aircraft components. Among these components are linear rails and bearings that allow for smooth motion of seats, armrests, and footrests.
- Aerospace Tooling and Machining: Utilizing linear motion guide systems in aerospace tooling and machining processes will enable accurate shaping and cutting of aerospace components. Reduced weight, increased fuel efficiency, and precise movement can all be achieved with linear systems.
- Satellite Systems: Linear motion components enable precise movements for satellite deployment mechanisms and solar panel positioning. They are often used in guidance systems, where high reliability and precision are critical. Linear guide systems can satisfy the demanding requirements and precision specifications for satellite positioning.
Linear Motion Components and Systems
Linear motion systems can be designed in various ways for every application. Nearly every linear motion system includes linear bearings, actuators, and slides. Linear motion systems include screw drives, linear motors, and linear guides. The most common materials used in linear motion components are varying metals, polymers, and composites. Every system can be designed to fit the exact specifications for the application.
Best Practices for Maintaining Optimal Linear Motion Performance
No matter the application, for optimal linear motion performance, proper care must be taken to maintain the system, including correct installation, alignment, lubrication, regular inspection and cleaning, and attention to the temperature and environment in which the linear guide system will operate. The more attention paid to these best practices, the more optimal the performance.
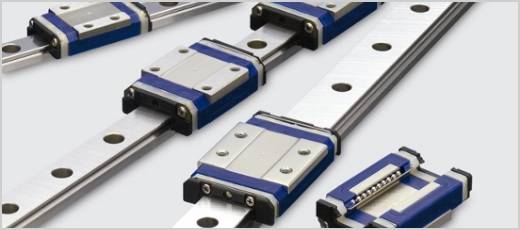
Proper Lubrication and Maintenance
In linear motion applications, bearings and guides require proper lubrication to ensure they are operating efficiently and effectively. A lack of lubrication can cause maintenance issues and even contribute to linear system failure. Simply acknowledging the need for lubrication is not sufficient. Selecting the right lubricant is important. Choosing appropriate lubricants based on the specific linear motion components used (such as ball screws, linear guides, or lead screws) will ensure smooth movement and reduce friction.
NSK provides grease and lubrication for all our linear guide products that are specified for optimal performance. For best results, establish a regular maintenance schedule for lubrication, taking into consideration usage frequency and environmental conditions. When building linear systems, consult with NSK for in-depth recommendations on lubrication and maintenance.
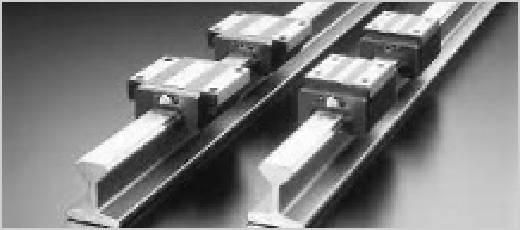
Regular Inspection and Cleaning
No matter how well designed and manufactured the linear guide system is initially, preventive maintenance and regular cleaning will extend the longevity as the system, as well as ensure optimal performance. When a potential issue is identified before it fails, the linear system can be adjusted and overall failure of the application is avoided. It is recommended to set up routine inspections to identify signs of wear, misalignment, or damage to the linear motion components.
Regular cleaning procedures will remove dust, debris, and contaminants that can impair motion efficiency, potentially leading to premature component failure. When the linear system is operating in an environment that is more prone to moisture, dust, or chemical contamination, cleaning and inspection should be done more frequently. When customizing the linear system for your particular industry and application, make note of the inspection and cleaning needs.
Correction Installation Techniques
Without correct mounting, positioning, and installation, a linear guide system cannot achieve optimal performance. Precision in installation is crucial. Improper mounting can add unnecessary strain, reducing the longevity and decreasing the precision and accuracy of the system. Ensuring precise alignment and positioning during installation will prevent uneven wear and strain on components. Adhering to manufacturer recommended torque specifications while securing bolts and fasteners will maintain the structural integrity of linear motion systems.
In addition, verifying the alignment of linear guides, screws, and other components will prevent binding, excessive wear, or reduced efficiency of the system. When installing the linear guide rail, the installation team must install in strict accordance with the specifications. Having an experienced and knowledgeable technician to handle installation can ensure that the system will function as needed.
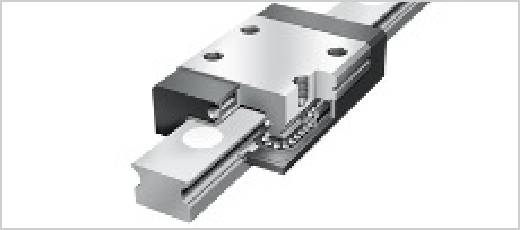
Temperature and Environmental Considerations
The environment in which your linear system will operate can impact the efficiency, effectiveness, and precision of the system. Operating temperature is a big factor in how the system will perform, due to thermal expansion and contraction brought on by extreme temperatures or wide shifts in temperature.
Managing the operating temperature within the recommended range to prevent thermal expansion or contraction, which can affect linear motion systems’ accuracy and performance. Depending on the application of your linear systems, the linear guide can be developed to operate within the accurate temperature range. The environment outside of temperature is also important to the optimal performance of a linear system.
Environments prone to dust, dirt, moisture, or chemicals can impact the performance of a linear system. It is recommended that seals and protective covers are implemented to shield linear motion components from environmental factors such as dust, moisture, and chemicals, which can cause corrosion and deterioration.
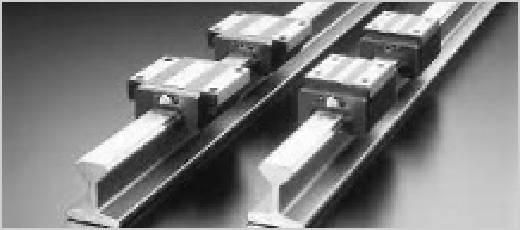
Aligning Linear Motion Components for Maximum Efficiency
Even with the best linear guide system, smooth, efficient, and precise linear motion cannot be achieved without proper alignment. Inconsistent or inexact alignment can reduce efficiency or even cause a system failure. Precision alignment ensures exact alignment and calibration of linear guides, screws, and related components specified to the system and application.
Every application has a different metric for precision. The operating environment of the linear system will also dictate the alignment specifications necessary, as some environments are more challenging. This precision alignment minimizes backlash and improves overall system accuracy. Alignment tools are often used to achieve optimal alignment, especially in complex systems with multiple linear motion components. Careful mounting of the linear guide is paramount when implementing linear systems, as proper alignment will help get the maximum performance and longest life from the linear guide system.
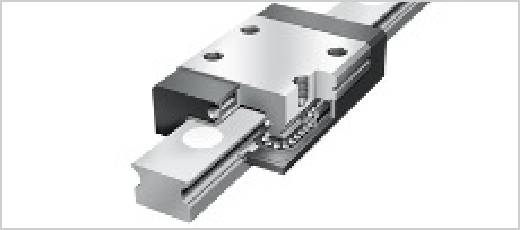
Avoiding Common Pitfalls in Linear Motion Design
For linear technology to work to the best of its capability, common pitfalls need to be avoided. Without first doing the research to determine the right system for your application, it’s possible to have a system that won’t perform as expected, which can have far reaching consequences for the end product.
One of the most common pitfalls is overloading the system. Overloading linear motion systems beyond their specified capacities can result in excess wear, deformation, or failure of the linear technology. When utilizing a linear motion system, make sure that capacity limits are respected.
The other common pitfalls many fall into is operator error. Like any technology, if the system is used or maintained incorrectly, the lifespan is greatly reduced. Providing training to operators and maintenance personnel to handle linear motion systems correctly will reduce the risk of accidental damage due to improper usage or maintenance.
Anything that needs to move in a straight line is linear motion, and linear systems ensure that the mass that needs guidance and support when moving is supported by linear technology. Linear technology reaches into nearly every industry, from the very simple and basic rail systems to the highly complex multi-axis systems found in highly precise technology.
The experts at NSK understand how to meet the specifications for any linear system needed by your industry and can assure our clients that their requirements are met. Our linear rail systems are precisely calibrated and designed for smooth and precise motion.